Responsive Space
SMARTSAT SPACELINK: A STUDY TO DEVELOP A PLATFORM FOR SPACE-READINESS
Partners in Infrastructure Resilience
Space infrastructure grows more critical to our society every single day. But that reliance comes with a major risk: disruptions in space infrastructure can be devastating, and it currently takes years to replace basic capabilities in orbit. We’ve taken part in a project designed to be prepared for future responsive space missions.
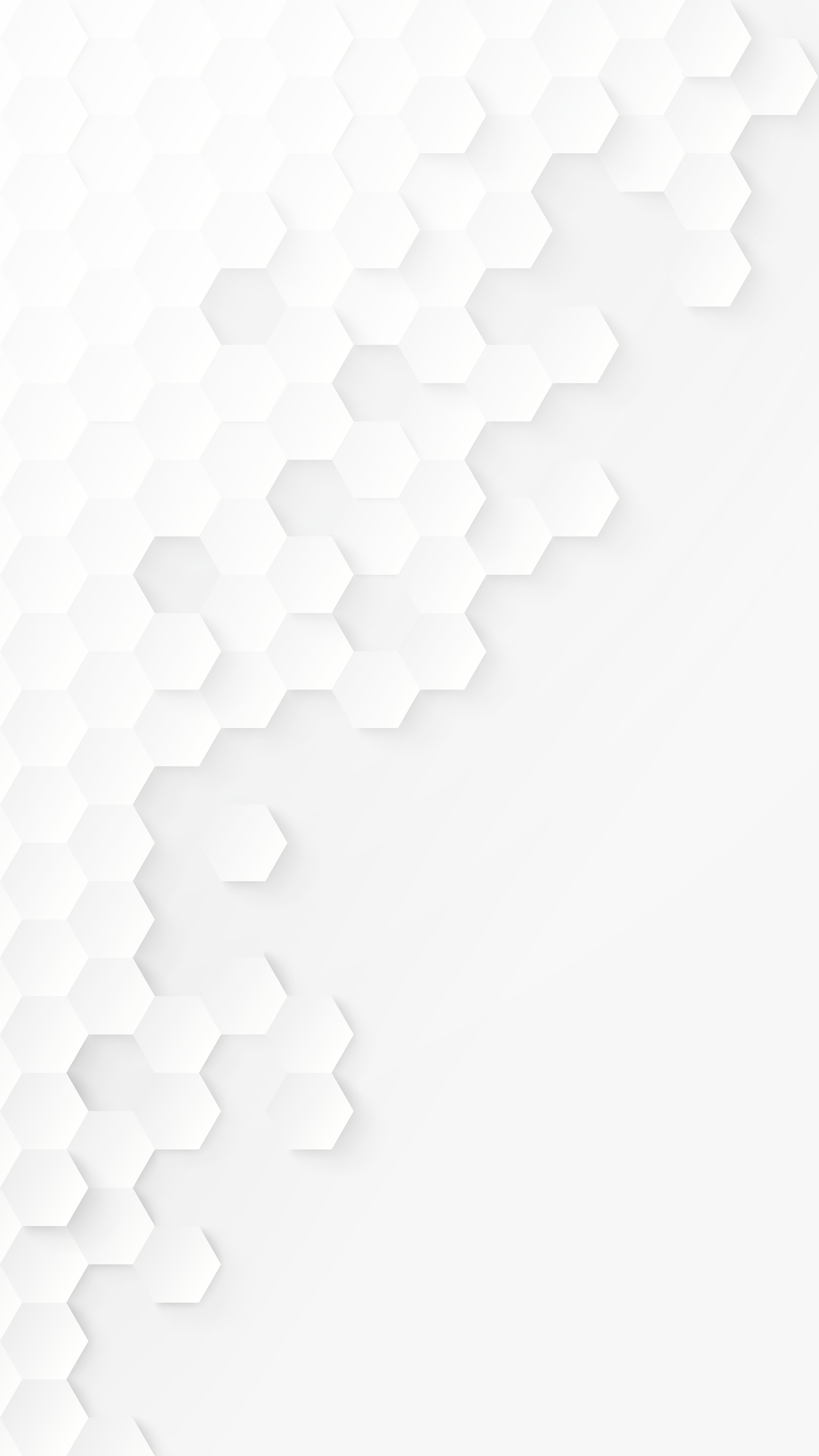
What is Responsive Space?
The Joint Air Power Competence Centre defines Responsive Space as:
Responsive Space is understood to be the ability to launch small satellites (up to 500 kg) on demand and on call into Low Earth Orbit (LEO) and to start operating within days, in order to reconstitute lost capabilities, augment existing – capabilities, fill unanticipated gaps in capabilities, and enhance survivability and deterrence.
Our Objective
Speed is everything when responding to an emergency in space. Our goal was to create a theoretical platform that could be quickly manufactured and launched to account for the difficulty in getting assets to space.
Reflex was responsible for designing the primary structure that all components would be placed on. This included defining the requirements needed to quickly source and install those components, designing a structure that could accommodate a “universal” but flexible payload of 20 kg, and building the box and software for the avionics unit.
Getting Into the Details
When looking into optimal solutions, we decided that CNC manufactured panels would be our best choice for our primary structure. They are well known, easily sourced, and extra qualifications wouldn’t be necessary in comparison to something that was 3D printed.
Similarly we knew the avionics unit needed to be flexible enough to manage different data requirements, and do so quickly.
When it came to brackets, we depended on the expertise of HPS. Their ability to utilize generative design and topology optimization software determined it would be faster to redesign and 3D manufacture their brackets as satellite bus components needed to be changed.
Our Findings
In May 2024, the SmartSat Spacelink platform, utilizing brackets from HPS and a laser terminal from Mynaric, successfully passed the vibration test and fitting for a launch with Isar Aerospace. The success of these tests show a readiness for responsive space missions and a platform capable of quickly delivering replacement assets to orbit.